Learn how to polish molds and the tools needed for polishing! Why is it recommended to automate mold polishing?
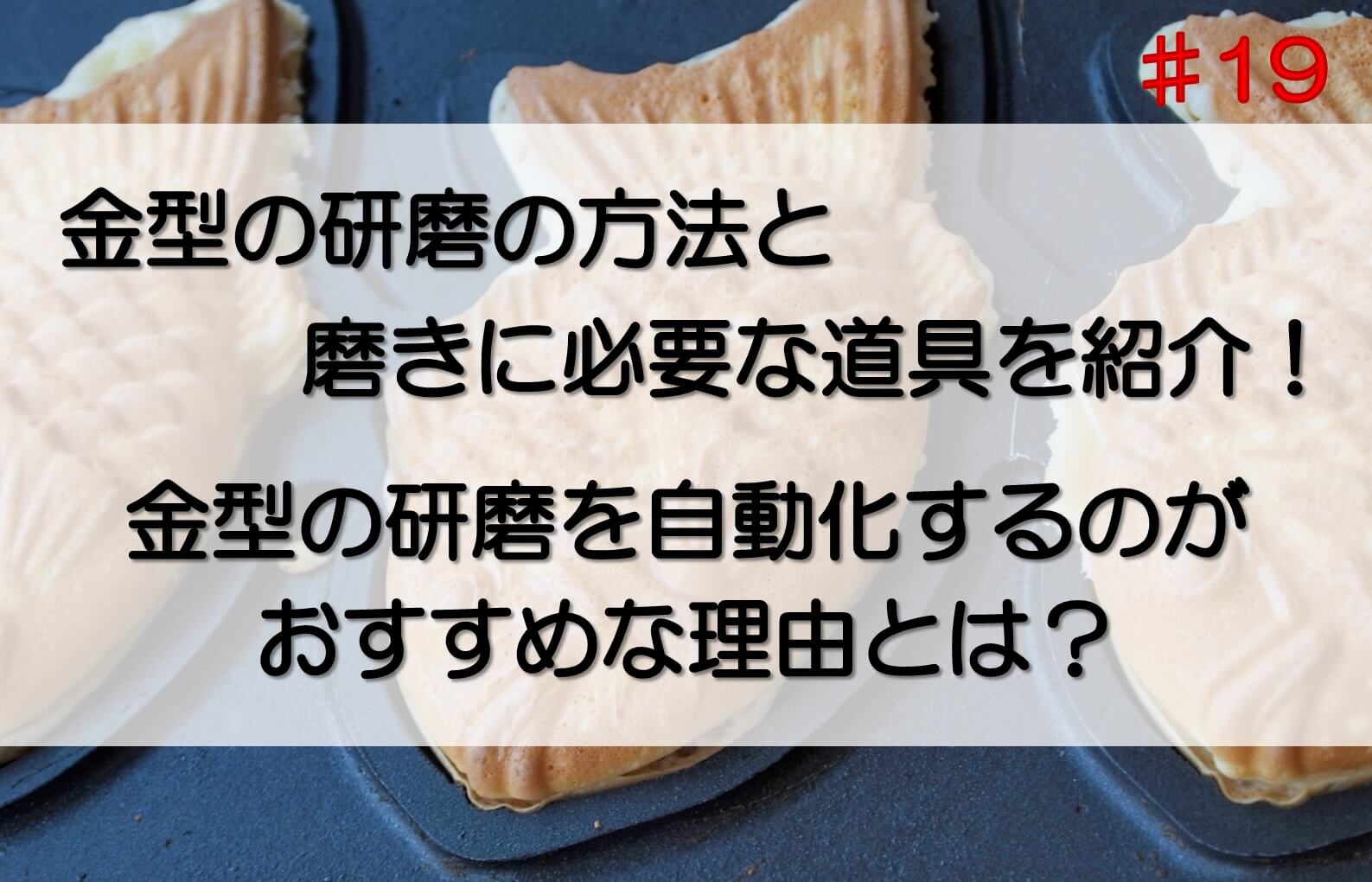
What do you do when you have to make a lot of the same thing?
It may depend on the degree of many.
For example, if there are three units, it is quite possible to make one of each.
So what if you need 200 units?
In such cases, "molds" play an important role.
Although "molds" are often referred to as the king of production engineering, their origins are surprisingly old.
Although not made of metal, there are records of "molds" already in use in ancient Egypt.
In this issue, we will introduce "molds," the driving force behind mass production.
Table of Contents
1. Are there any advantages to using molds? What are the characteristics and materials of molds?
2. Is it true that polishing is necessary for the production of molds?
3. What is the method of mold polishing? Why is finish polishing done by hand?
4. Automation of mold polishing is ideal for cost reduction
5. Automate mold polishing for more efficient production!
1. Are there any advantages to using molds? What are the characteristics and materials of molds?
Many people are familiar with the term "mold," but few have actually seen one in person.
Think of the mold used to bake taiyaki.
A mold is a die used in the mass production of a product.
Products here are made of a variety of materials, from metal to resin (plastic).
Consider the advantages of using molds!
Let us consider a situation where 200 units of a certain product are to be manufactured.
・Handmade: 60 min/unit
・When using molds: 15 min/unit
If all 200 units are handmade, a simple calculation shows that it would take 60 minutes x 200 units = 200 hours.
However, the use of molds shortens the molding process, so each unit can be finished in 15 minutes.
In other words, it can be finished in 15 minutes x 200 units = 50 hours (1/4 the time compared to manual work).
Advantages of Using Molds
・The ability to significantly reduce the time required for production
・Differences between individuals are difficult to detect.
This means that once a mold is made, the product is always the same according to its shape.
Therefore, the molds must always be highly precise.
If the mold dimensions are inaccurate, of course the product will also be inaccurate.
It is no exaggeration to say that the mold determines the quality of the product!
What are molds made of?
There are several types of molds, depending on the method of use (stamping, forging, or casting).
For example, in the press process, material is placed in a die attached to a press machine and clamped between the dies to form the material.
Therefore, press dies are designed to resist pressure and impact.
In addition, heat resistance is required because molds are subjected to high temperatures during the casting process. Most molds are made of "high-alloy tool steel.
Highly alloyed tool steel" is an unfamiliar name, but a simple explanation is that it is an alloy of several metals (elements).
Highly alloy tool steels" are carbon tool steels to which tungsten, molybdenum, chromium, silicon, vanadium, nickel, etc. are added.
The alloy is intended to improve impact resistance and heat resistance.
Cemented carbide (an alloy made by sintering hard metal carbide powder) and ceramics are also often used for molds, although at a slightly higher cost.
2. Is it true that polishing is necessary for the production of molds?
How are molds manufactured?
As mentioned above, molds are indispensable to the manufacturing process, but the manufacturing process is extremely precise.
Basically, 95% or more of the total is formed by cutting with a machining center, etc., using "high-alloy tool steel" and "cemented carbide" as raw materials.
The remaining 5% is adjusted by finish polishing. This 5% adjustment is critical, and the accuracy of this process directly affects the quality of the product produced.
Cutting?Polishing?Don't they both mean the same thing? I recommend this article to anyone who wonders.
What is cutting??Let's know the purpose and method of cutting process.!~What is the difference between grinding, cutting, and polishing? Find out what the words for grinding and polishing mean!~ part3 ~ - Sankyo Rikagaku Products (fujistar.com)
The finishing polishing process is intended to remove burrs and adjust surface roughness during molding.
The cutting process uses automatic grinding machines with grinding wheels, whereas much of the polishing process is done by hand with stick-type grinding wheels and small rotary tools.
3. What is the method of mold polishing? Why is finish polishing done by hand?
As explained earlier, mold forming is mainly done by cutting.
In many cases, the workpiece is machined to near the set dimensions, and then finish polished by hand for fine tuning.
There are several reasons why finish polishing of molds is not mechanized and is done by hand.
・Molds are made in small quantities and in a wide variety of products.
Since molds are made according to the products to be produced, it is natural that the number of types of molds will increase.
Furthermore, we do not manufacture many molds of the same shape.
When grinding is automated, the machine must be initially set up to determine which and how much of each part with different shapes will be ground.
When producing different shapes, the initial setup of the machine is required each time.
・High precision required for finishing and technical skills
Molds require a high degree of precision in finishing.
In some cases, it is necessary to finish to a mirror surface, which requires a lot of time and technical skill.
Because of the high degree of difficulty and delicacy of the work, it cannot be easily mechanized.
Finish polishing of molds is divided into three major processes.
・rough-hewn
・half-finished
・Final Finishing
In rough finishing, burrs from the cutting process are removed.
It is recommended that abrasive materials used be grindstones or other abrasive materials with long-lasting sharpness.
If you are having trouble with mold deburring, please also see this page.
I want to remove burrs cleanly by polishing! Points for deburring metal and resin that directly affect the finished product - Sankyo Rikagaku Products (fujistar.com)
In the medium and final finishing processes, rotary tools such as buffing tools are used to adjust surface roughness.
To further bring the surface closer to a mirror surface, use a liquid polishing compound such as compound.
4. Automation of mold polishing is ideal for cost reduction
The fabrication of small-quantity, high-mix molds relies heavily on the technical skills of workers because of the lack of automation, and it was not a task that could be done by just anyone.
However, recent years have seen remarkable advances in machinery, making it possible to automate polishing even for molds that require technical expertise for small-lot, high-volume production.
Advantages of Automated Mold Polishing
・Reduction of work time
Integrated automation from deburring to finishing reduces the time required for manufacturing and enables cost reduction.
・Stable quality
Since the machine automatically polishes the surface, polishing can be done more evenly than when done manually.
・Effective use of human resources
Sankyo Rikagaku's blower blast can not only automate polishing, but can also be customized to suit the shape of the customer's workpiece.We are able to pursue the finish that our customers want.
・All-in-one and space-saving
・Inverter-controlled jet air velocity can be freely set
・Efficiently handles partial burr removal
・Increased number of nozzles and reduced processing time
Automating mold polishing offers many advantages.
Please feel free to contact Sankyo Rikagaku if you are interested.
5. Automate mold polishing for more efficient production!
In this article, we briefly introduced mold polishing.
Although seemingly unassuming, molds are an indispensable element of the manufacturing industry and play an important role in determining product quality.
In addition, machine automation of mold polishing may improve quality and reduce costs.
Please feel free to contact Sankyo Rikagaku if you are interested in automating the grinding and polishing of molds.