What is an abrasive, and what are the purposes and merits of DIY and plastic model polishing?
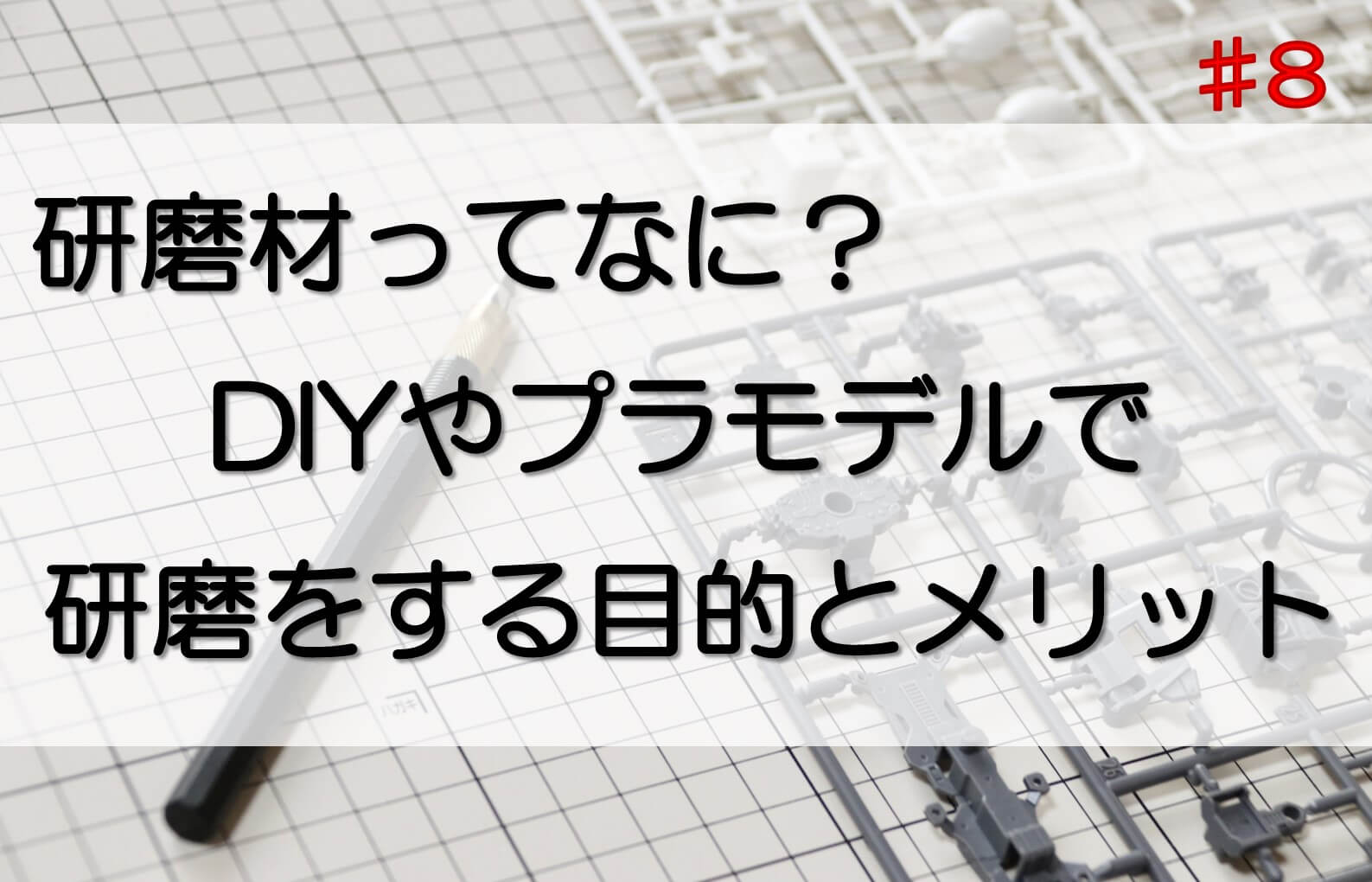
These days, DIY and plastic models are attracting attention due to the demand for nest eggs,
I can't believe that knowing the basics of polishing makes a difference in the finished product. ......
In fact, it does appear!
The tip of a square piece of wood purchased at a home improvement store is smooth and clean.
As soon as you saw it yourself, the cut ends up jagged and thorny.
The cross section of that square timber has countless spines, and if left unattended, injury is inevitable.
This is where abrasives come into play!
Using sandpaper, the jagged cross section is polished to a smooth and clean condition.
This step not only prevents unintentional injury, but also greatly increases the level of finish.
You there who think it's okay to paint it later!
Just by adding a polishing process before painting, paint adhesion is greatly improved!
Let's learn about the basics of abrasives in order to 1-up your DIY project.
Table of Contents
1. What are abrasives, and what is the purpose and benefit of abrasive processing in DIY and plastic modeling?
2. I want to try abrasive processing in DIY and plastic models! Brief explanation of the structure of abrasives
3. Teaching how to choose abrasives for DIY and plastic models! Will the right abrasive improve the finish?
4. 3 Sankyo Rikagaku abrasives recommended for DIY and plastic models
5. Let's use the right abrasive for the right application in DIY and plastic models to raise the level of your work!
1. What are abrasives, and what is the purpose and benefit of abrasive processing in DIY and plastic modeling?
What is an abrasive in the first place?
There are various types of abrasives, but generally speaking, abrasives are made by bonding fine particles called abrasive grains to a base material (kizai), and the unevenness of the grains makes polishing easier to understand.
The polishing process using abrasives is generally called "polishing process." The polishing process can even out uneven surfaces of products, remove burrs, and even give them a shiny, mirror-like finish.
The polishing process reduces surface irregularities and creates a shiny, almost mirror-like surface, which improves appearance and prevents rust and dirt from adhering to the surface, creating various added values.
For this reason, many manufacturing sites have also introduced polishing as a final process to improve the quality and appearance of their products.
However, the polishing process is not only used in manufacturing!
Cutting is an essential task in DIY and plastic modeling.
Polishing is then added, which greatly improves the appearance.
Some may be surprised to learn that
Advantages of Polishing Process
・Can improve appearance by smoothing the surface
・Can remove surface rust and dirt
・Can be used not only to remove old paint film but also for pre-treatment before painting (improves paint adhesion)
・Allows final adjustment for accuracy
Many of you may be thinking that if there are so many advantages to polishing after only one operation, you may want to try it.
Let's start polishing! But even if you think so, you may be wondering which abrasives to choose from among the many available. The following is an introduction to the basic structure of abrasives and how to choose the right one.
2. I want to try abrasive processing in DIY and plastic models! Brief explanation of the structure of abrasives
In the polishing process, a variety of materials are targeted, from plastics and other resins to metals and wood.
Some of you may be wondering how abrasive materials are made that can shave metal and stone, which have a very hard image, aside from relatively soft plastic and wood.
Earlier, we explained that abrasive materials are composed of fine particles called abrasive grains bonded to a base material (kizai).
Let's look at the structure of abrasives in just a little more detail.
a) Base material
Mostly paper, cloth and film, these are the main parts of abrasive materials.
b) Adhesive1
Adhesive is used to fix the abrasive grains to the substrate.
c) Abrasive grain
Abrasive grains are the main component of abrasive materials. Abrasiveness varies greatly depending on the grain size and type of abrasive.
d) Adhesive2
To hold the abrasive grains firmly in place so that they do not fall out during polishing, they are hardened once again with an adhesive. The type of adhesive used will greatly affect the performance of the polishing process.
e) (Anti-clogging agent)
Abrasives used in dry grinding may have an anti-clogging agent applied to the top surface layer to prevent clogging (a phenomenon in which shavings interfere with grinding).
Many of the sandpapers that everyone is familiar with also have this structure.
It is amazing how many layers are coated on top of each other even though they look as thin as paper.
We will give you some pointers on selecting abrasives based on this structure!
3. Teaching how to choose abrasives for DIY and plastic models! Will the right abrasive improve the finish?
3 points to choose abrasives
(1) Shape
(2) Grain type
(3) Grain size
If you keep these three points in mind, you will have a much better chance of finding the abrasive you are looking for.
Let's take a closer look at each in turn.
(1) Shape
First, consider the size of the object you wish to shave.
For example, in the case of a plastic part of about 5 cm, it is expected that a better finish will be obtained by sanding a small area by hand, since it is a small area to be sanded. It is recommended to use sandpaper cut to the desired size.
On the other hand, if you want to polish the entire surface of a 2-meter thin steel plate, you will lose days by hand.
Choose abrasives with a sealed or Velcro finish that are attached to a sander or other air (electric) polishing tool.
(2) Base material and abrasive grain type
Next, select the base material and abrasive grain type.
What is important at this point is the material of what you want to polish and the purpose of the polishing.
First, the material. Roughly speaking, if it is plastic, wood, or paint (coated with paint), there is no problem in choosing a common sandpaper.
The use of film-based abrasives in the finishing process will result in a more precise finish.
On the other hand, if you want to scrape relatively hard objects such as metal, a cloth file is recommended because it is more durable.
In addition, there are various abrasive grain types such as brown alumina (A), white alumina (WA), black silicon carbide (C), green silicon carbide (GC), zirconia, ceramic, and diamond, to be explained in detail, but we will briefly explain how they are used.
Consider your polishing objectives.
Use abrasives with sharp and cutting abrasive grains such as brown alumina (A) and white alumina (WA) for rough scraping such as rust removal and pre-paint preparation.
In contrast, if you want to achieve a glossy finish or mirror finish, abrasives using black silicon carbide (C) or green silicon carbide (GC) can be polished to a better finish.
Zirconia, ceramic, and diamond are used primarily when polishing hard metals.
(3) Grain size
Finally, the granularity greatly affects the degree of completion.
Grain size refers to the size of the abrasive grains. The larger the grain size number, the finer the finished abrasive. Although a wide range of grain sizes are available, from #12 (coarse) to #20000 (fine), it is useful to keep in mind the following rough specifications: rough polishing (up to #400), medium polishing (#500 to #1200), and finish polishing (#1500 to #1500).
Prepare multiple grit sizes in advance and try them on inconspicuous areas before actual use to find your preferred finish.
By the way, do you know a formula that is useful when you want to know the approximate size of a grain?
<15000÷granularity> can be obtained.
(e.g.) For abrasive grains of grain size #400, 15,000 ÷ 400 = 37.5, and the approximate size of the abrasive grains is about 38 microns.
4. 3 Sankyo Rikagaku abrasives recommended for DIY and plastic models
Sankyo Rikagaku is known for this! Long Seller Products
Recommended Product 1: Water Resistant Abrasive Paper (Sankyo Rikagaku Co.)
Is it the most common water-resistant paper?
— Pocket’s Gunsmithing@スチェキン、ハイスタH-Dミリタリ&猫に関するツイート (@PocketPistolPTY) December 4, 2020
Sankyo Rikagaku and FUJI STAR brand water-resistant sandpaper.
I'm glad to see that we have a variety of counts, from coarse to fine.
The #320 and #500 are also moderately useful. pic.twitter.com/V0XgoFrYbd
The secret of its popularity is that it is available in a wide range of grain sizes and can be purchased in small quantities.
The LCCS series is especially soft and conforms to curved surfaces, making it ideal for detailed work such as plastic models.
Sankyo Rikagaku's LCC sandpaper finally secured...pic.twitter.com/shn5jx5mVH
— シュテル(旧:狸丸)@オメガモンX抗体製作中 (@stern_modeling) November 14, 2021
Just polishing at the end gives it a different look.
Recommended Product 2: Ultra-precision polishing film (Sankyo Rikagaku Co.)
Strobe surface on the back. Polished with plastic polishing film. #4000
trinomial chemistry Ultra-precision polishing film Pack of 4 #4000 https://t.co/uLvQwHVkWZ pic.twitter.com/FlwFmVKgRs— kk (@sl_1200a) September 29, 2019
Like water-resistant abrasive paper, it can be cut and used only as much as you want to use, so it is very cost-effective!
Amazonで三共理化学 超精密研磨フィルム 10000番 買ったのが届きました。アケコンの天板が傷だらけなのでどうしようか考えて磨くことにしたんですよ。で最初はコンパウンドを買おうと思ったんだけどこっちが面白そうだったのでこれにした。 pic.twitter.com/N5kTgVEzpv
— MaskedRiderZ (@kaizer_zero) August 2, 2019
It is sure to be of great use from rust removal to footing, which is a preparation for painting.
Recommended Product 3: Kenmaron (Sankyo Rikagaku Co.)
Kenmaron Super is still the best rust remover.(*‘∀‘)#yokoito#kyoto pic.twitter.com/7ocNT3Am3d
— 足立 正 (@ohmistar) October 18, 2019
The nylon non-woven fabric is coated with abrasive grains to maintain excellent grinding performance and prevent clogging.
Because of its excellent elasticity, it blends well even on curved surfaces.
It can also be used as a preparatory footing for painting, making it a perfect item for painting after rust removal.
I had to peel off the peelable paint in prep for painting the wheels tomorrow, but it stuck more than I thought it would, so I struggled.
The rest is ready for polishing with Kenmaron.pic.twitter.com/6QHP8CEanO— さうす (@N3_Bl5) May 3, 2018
5. Let's use the right abrasive for the right application in DIY and plastic models to raise the level of your work!
In this issue, we introduced Sankyo Rikagaku's abrasives, which are useful for DIY and plastic models, from basic knowledge of abrasives.
By incorporating polishing into your manufacturing process, you can be sure that your work will be of even higher quality.
It is also important to select an abrasive that matches the object and the desired finish.
At first glance, abrasive materials may seem unobtrusive and rarely in the limelight, but in fact, they are an important content that supports manufacturing.
Sankyo Rikagaku Products has been manufacturing and researching such abrasives for more than 90 years and produces many high quality abrasives produced domestically.
We have a wide lineup of grain sizes, so we can offer the ideal finish to your liking.
If you are interested in polishing, please feel free to contact Sankyo Rikagaku.