I want to remove burrs cleanly by polishing! Points for deburring metal and resin that directly affect the finish!
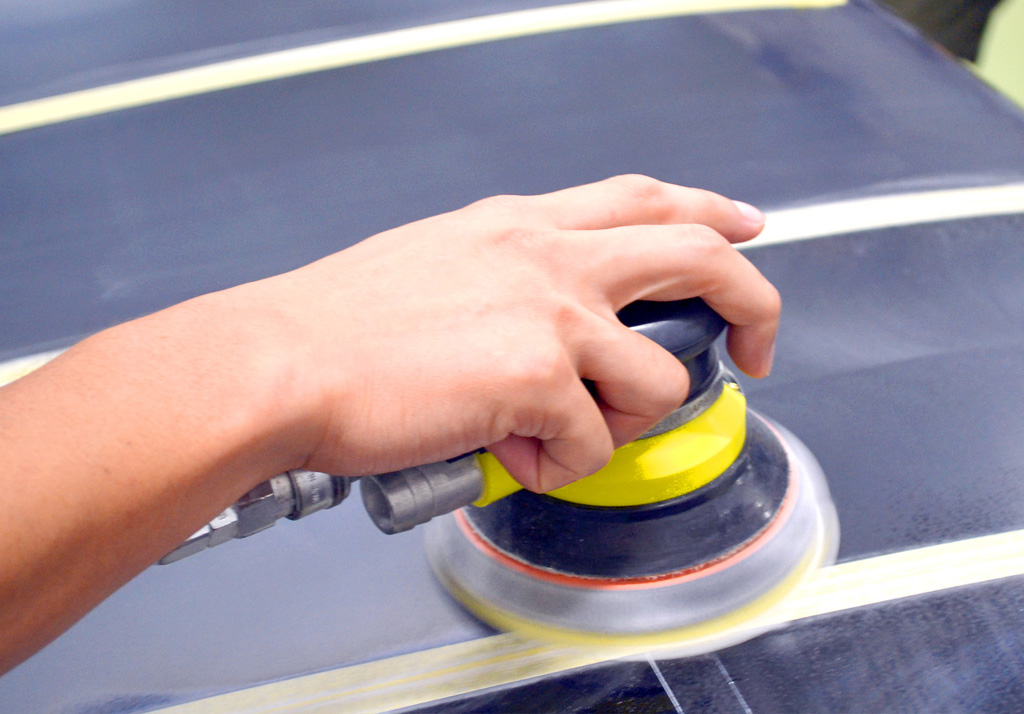
I am sure that many of you have experienced that when you finally finished and took a break to take a closerlook at the workpiece, you found that there were still some jagged edges.
The jagged edges are actually burrs.
It doesn't look good if burrs remain, and we would like to clean them up if we can.
Deburring" represents the process of removing burrs and is an "important process" that determines the accuracyand safety of the product.
In this issue, we will explain about deburring (removal of burrs).
Table of Contents
1.What is burr removal by polishing, and what kind of burr occurs in metals and resins?
2.Advantages and effects of deburring by polishing to remove burrs
3.I want to remove burrs! Methods of deburring that can be done by grinding and their advantages anddisadvantages
4.How to remove burrs efficiently by polishing - Leave it to Sankyo Rikagaku for deburring!
5.You want to remove burrs! If so, optimize your deburring process with our deburring equipment!
1. What is burr removal by polishing, and what kind of burr occurs in metals and resins?
Burr" refers to the jagged edges of a machined part that occur when metal or resin is processed.
Burrs also occur when plastic or rubber is processed, regardless of the material,
In the manufacturing process of a product, there is always a process called "deburring" to remove burrs.
In the deburring process, it is necessary to remove only the burrs without changing the shape of the workpiece.
It is a process that rarely attracts attention because it does not involve bold processing that significantlychanges the shape of the product,
It is also a very important operation that directly affects the quality and performance of the finished product.
It is no exaggeration to say that the accuracy of deburring determines the final quality.
2. Advantages and effects of deburring by polishing to remove burrs
Attempting to remove burrs increases the number of steps and takes longer to complete.
However, if burrs created during processing are left untreated,
Many risks would be incurred.
・Does not perform as expected
Unexpected behavior such as friction caused by interference of burrs left on parts during drive,
It may not perform as expected.
・Not finished to standard size
If burrs remain, the part will not fit into the designed size and will be less accurate when assembled.
In some cases, the gaps created by burrs prevent parts from meshing, making assembly impossible.
・malfunctions
Burrs may fall off and enter the operating section due to impact during use.
This can cause damage or clogging of the machine, leading to malfunction of the machine itself.
・hurt
The tips of burrs are very sharp and dangerous. There is a risk of injury by touching them with bare hands.
Removing burrs not only improves appearance, but also avoids these risks.
3. I want to remove burrs! Methods of deburring that can be done by grinding and their advantages anddisadvantages
Burrs are an inevitable part of machining, and although they can be suppressed, it is difficult to eliminatethem completely.
In deburring, there are the following major methods.
・Manual work using abrasives and special tools
:Visually check for burrs and remove excess portions.
Advantages:It can be done while visually checking, thus avoiding overshaving.
demerit:It is time-consuming as well as subject to variation among workers.
・Barrel polishing
:Parts and abrasive are fed into the barrel container, and burrs are removed by rotating or vibrating thecontainer.
Advantages:A large quantity can be processed at a time.
demerit:Because of random polishing, it is difficult to maintain high precision and there is a risk of excessscratches.
・Buffing (brush polishing)
:The workpiece is placed against a buffing wheel or brush rotating at high speed to remove burrs.
Advantages:Burr areas can be removed reliably, and furthermore, it is possible to continue and finish to a mirror surface.
demerit:Adjustments are necessary depending on the angle and force, and require skilled technical skills.
・blast (from explosion)
:Abrasive is sprayed at high speed and applied to the burr area to remove it.
Advantages:Fine adjustment of the processing range is possible, and processing can be done in a shorter time than by hand.
demerit:A certain amount of capital investment is required.
4. How to remove burrs efficiently by polishing - Leave it to Sankyo Rikagaku for deburring!
Sankyo Rikagaku's Blower Blast is ideal for deburring with the following features.
・All-in-one and space-saving
・Inverter-controlled jet air velocity can be freely set
・Efficiently handles partial burr removal
・Increased number of nozzles and reduced processing time
Furthermore, when used in combination with Sankyo Rikagaku'sLappinmedia, it can be used for deburring (fine) and polishing.
The greatest feature ofLappinis that polishing proceeds as if gliding, enabling removal of only fine burrs without deep scratches on thesurface.
Only burrs can be removed without roughening the surface more than necessary.
Sankyo Rikagaku's blower blasting is also highly compatible with automation, and the selection of abrasivematerials allows us to pursue the desired finish for our customers.
<Advantages of Automated Deburring>
・time reduction
・Quality Stability
・Effective use of human resources
Automating deburring offers many advantages.
Please feel free to contact Sankyo Rikagaku if you are interested.
5. You want to remove burrs! If so, optimize your deburring process with our deburring equipment!
In this article, we briefly introduced deburring (removal of burrs).
Deburring may seem like an inconspicuous operation, but it is one of the most important processes in productprocessing.
By improving the deburring process, which cannot be separated from the production floor, it may be possible toimprove quality and reduce labor costs.
If you are interested in deburring, please feel free to contact Sankyo Rikagaku.