What are milling and slitting processes? A brief explanation of the types of metal cutting processes and their advantages and disadvantages!
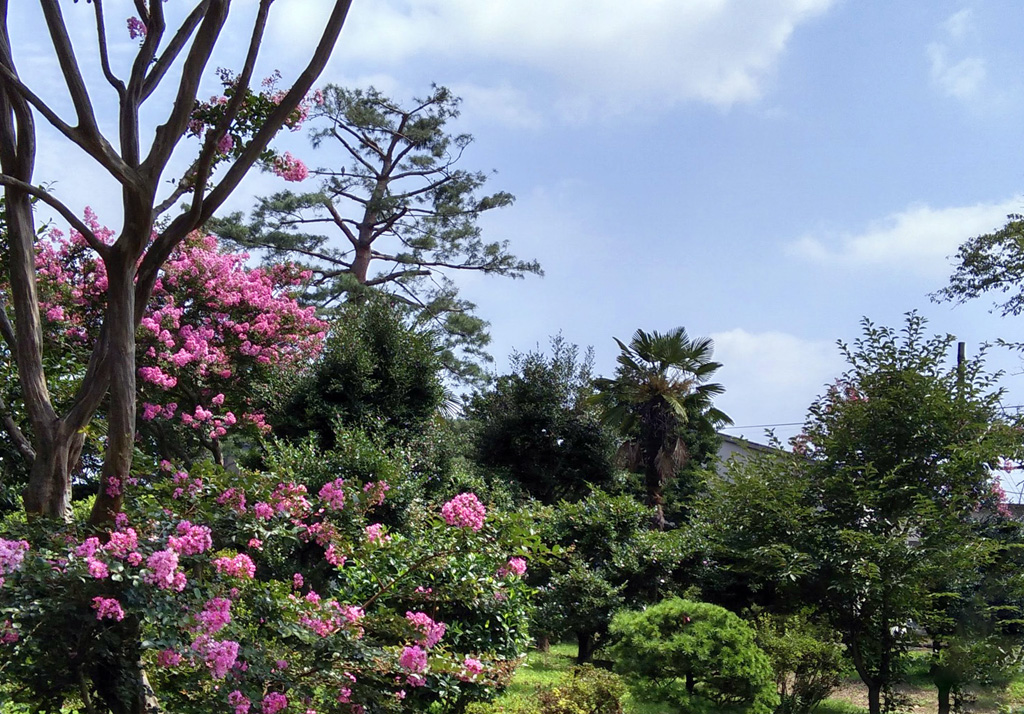
What do you think of when you hear the words "metal cutting"?
Some may be surprised at how easily hard-looking metal can be sharpened.
Certainly, it is understandable that even the hardest metals can be sharpened by even harder ones.
However, most tools used in cutting operations are made of metal, as is the work material.
In fact, it is possible to sharpen metals as smoothly as a pencil by applying a large force to a very smallcontact area.
Also, when we hear the word "metal cutting," we tend to imagine a rough finish, but in fact, cutting is a veryconvenient method that can accurately process even small, complexly shaped parts.
In this article, metal cutting will be briefly explained.
Table of Contents
1.What is metal cutting? Cutting process has many types and benefits!
2.What are the types of metal cutting operations and how are they done? What kind of work is milling?
3.Are there any advantages or disadvantages of metal cutting?
4.Sankyo Rikagaku's finishing process is ideal for metals after cutting
5.summary~Learn about metal cutting and expand your machining capabilities.~
1. What is metal cutting? Cutting process has many types and benefits!
Metal cutting is the process of shaving a material using a machine tool to bring it to a desired shape.
Cutting includes shaving, of course, but there are also drilling, keyway machining, and a wide variety of othermachining methods.
This makes it possible to produce precise and variously shaped parts.
Furthermore, the tools required will vary depending on the process.
First, let us briefly introduce the types of cutting processes.
2. What are the types of metal cutting operations and how are they done? What kind of work is milling?
Cutting processes are broadly classified into the following three types.
◆Rotary disk machining
This method involves rotating a fixed material on a lathe and applying a tool to it to shave it.
(processing example:Bolts, shafts, connectors etc)
◆milling
In this method, a material is fixed to a milling machine, which processes the material by moving a bladerotating at high speed.
(processing example:Keyway grooving, slitting etc)
◆drilling
This method uses a rotating tool to drill holes in the material.
(processing example:Bolts, screws etc)
3. Are there any advantages or disadvantages of metal cutting?
<Advantages>
Hardly limited by material thickness
Material thickness is usually important in stamping and sheet-metal processing, but in cutting, as long as thesize is within the machining range of the machine, it can be processed regardless of thickness or shape.
Precise processing is possible
Cutting, which is basically controlled by computer, allows for precise design reflection and fine-tuning ofsize.
No mold is required and can be produced from a single piece.
No molds are required, and can be produced from a single piece using only blueprints. Initial investment can bereduced.
<demerit>
Processing takes time
Cutting takes time to produce due to the nature of the process, which involves machining the product whilecutting the material.
Therefore, it is not suitable for mass production as in die machining.
Another disadvantage is the relatively high cost per unit.
4. Sankyo Rikagaku's finishing process is ideal for metals after cutting
Do you have trouble with processing after the desired shape has been achieved by cutting?
Sankyo Rikagaku can propose solutions to further finish your workpieces to a mirror finish.
For example, with tape polishing, the roughness can be adjusted without destroying the shape of the workpiece.
The thin base material and uniform abrasive grains ensure a consistently good surface finish.
It is also highly compatible with automation, and the selection of abrasives allows us to pursue the desiredfinish for our customers.
ABRASIVE PRODUCTSCONTACT US
5. summary~Learn about metal cutting and expand your machining capabilities.~
In this article, we briefly introduced the metal cutting process.
There is a suitable method for each cutting process, and when designing, just knowing the tooling and machiningmethod is enough.
It may be possible to reduce production costs.
In addition, new added value can be added by finishing the workpiece more precisely after cutting.
If you are interested in polishing, please feel free to contact Sankyo Rikagaku.